Truck with pantograph
from RWTH Aachen
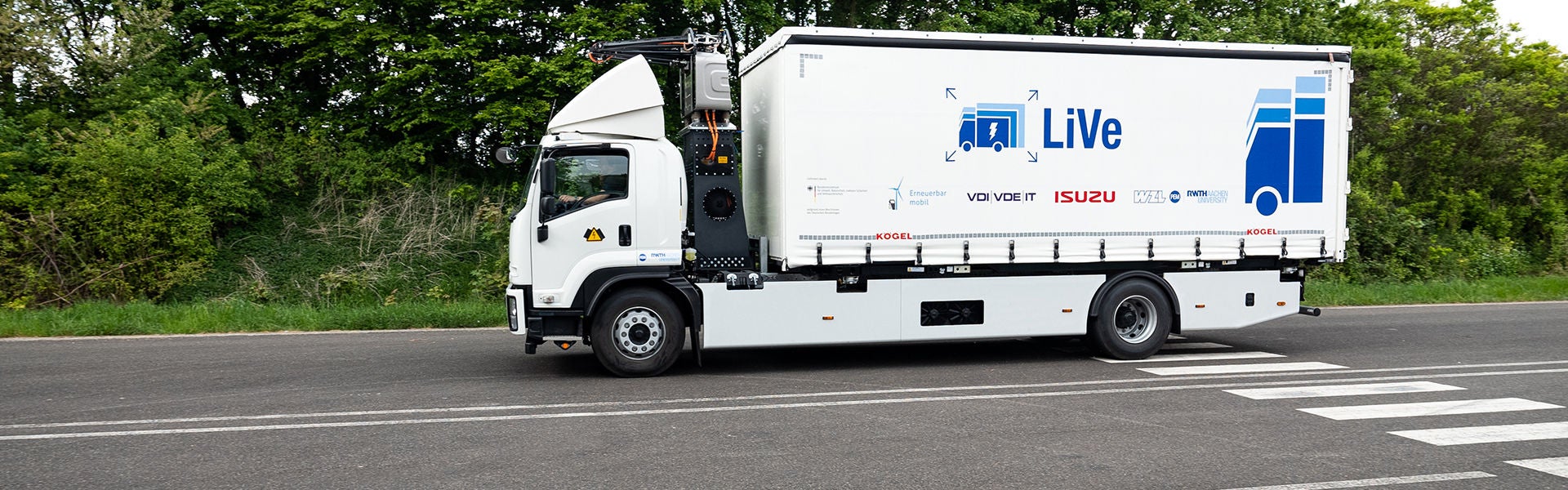
Innovative research project from the RWTH Aachen University
The PEM of the RWTH Aachen University is developing electrified trucks with pantographs and Webasto components to sustainably reduce CO2 emission on the roads worldwide. Road transportation is also crucial for a significant and lasting reduction of CO2 emissions in the traffic turnaround. Trucks are responsible for roughly ten percent of global CO2 emission. At the same time, they are difficult to electrify due to their high energy requirements as well as the long distances they have to travel.
An effort to change this and find a competitive solution for freight transport is being carried out by the Production Engineering of E-Mobility Components (PEM) chair at RWTH Aachen University, which is conducting research in precisely this area. As part of the LiVePLuS project, the chair specialists developed an electric drive train with pantograph and battery and implemented it in a first prototype with the support of Webasto, system partner for electromobility.
Founded in 2014, the PEM chair of the RWTH – one of the universities of excellence in Germany and top universities worldwide – is studying the core components of electromobility. Four research groups are focusing on the battery as one of the core components of the electric drive train across the entire value chain. "Our goal is to develop new ways to actively save CO2 emissions. Road traffic is responsible for a large percentage of the emissions.
If we take a closer look, we find that it is primarily the heavy commercial vehicles whose electrification would have a considerable impact on CO2 reductions. So for maximum efficiency and the greatest possible impact, this is precisely the area that we want to focus on in our research projects," explains Konstantin Sasse, Team Leader Battery Engineering & Safety at PEM.

Making traffic turnaround possible
The main objective: to develop adaptable modules of drive train building blocks that can be individually adapted to the application area. And so the LiVe project was launched in September 2017 that initially studied various technologies such as the fuel cell or pantograph – a fold-out current collector mounted on the vehicle – on the basis of the battery-electric vehicle. The project LiVePLuS was then created on that basis in February of 2020 and focused on heavy trucks with battery and pantograph.
To validate the research results and demonstrate the suitability of semitrailer trucks with pantographs, a truck was also to be retrofitted as a prototype. This classically consists of an electric motor and traction battery to which is added the pantograph as an interface to an overhead line system. A sensor system detects if the vehicle is traveling in a traffic lane with overhead line and the truck's pantograph extends and docks with the overhead line. This supplies the electric motor with power and charges the battery at the same time.
Both projects are sponsored by VDI/VDE Innovation + Technik GmbH, and they are funded by the German Federal Ministry for the Environment, Nature Conservation, Nuclear Safety and Consumer Protection (BMUV). "The technology with pantographs is particularly interesting as the infrastructure for it can be implemented rather promptly – much can already be achieved here by 2030. Studies have shown that by using overhead line trucks, around 50 percent of CO2 emissions can be cut down by 2030 compared with conventional trucks. If one takes this calculation further and operates the overhead line systems exclusively with renewable energy sources, the pure operation of these trucks would be CO2 neutral already today," states Simon Dünnwald, Team Leader E-Mobility Production Engineering of PEM.
The energy supplied by pantographs is not only very efficient due to its high overall efficiency, but there are also only few disadvantages compared with conventional trucks. The impacts on the infrastructure are similarly low: Traffic lanes with overhead lines can also be used by other traffic participants without restriction. Such overhead lines are currently already installed on segments of the A1 and A9 autobahns as test routes. "Simulations and studies show that retrofitting around 30 percent of the German autobahn network – some 3,200 to 4,000 kilometers – with overhead line systems is enough to electrify 80 percent of heavy trucks. So we have an enormous potential here," says Dünnwald.

Components and first-class support from Webasto
Since there are presently no pantographs truck with pure electric power operating on German roads, and the technology is thus very new, the research group was unable to resort to an already ready-to-run system and had to find innovative solutions instead. The delivery of the components also proved to be challenging. "We are building prototypes in correspondingly small quantities for our research project. This is not attractive enough for many suppliers. Technical availability and delivery times of the individual components also had to be appropriate.
The application field of heavy commercial vehicles already excludes some market participants. And of course we had some requirements regarding the components. For example, instead of prototype batteries, we wanted to install batteries certified for series production that are compatible with the rest of the high voltage on-board power supply," explains Sasse. Because space is limited in the truck, the size of the batteries also had to be appropriate. After intensive market scrutiny and in-depth research, the choice finally fell on Webasto's standard battery for commercial vehicles.
The company was not only able to supply the required components at short notice, but also provided active support with its expert knowledge. "We exchanged ideas closely with Webasto and have direct contact with all departments. Developing a prototype always means that very specific questions come up for which we need the opinions from experts. We worked very closely with Webasto, received prompt feedback, received all relevant data and even received support during commissioning of the individual components on site," explains Sasse.
In addition to the battery system from Webasto, the Vehicle Interface Gateway (VIG) was also used on the product side. It is very compact and serves as interface between vehicle and batteries and allows the control of up to 16 batteries. The research group developed the so-called Power Distribution Unit (PDU) on the basis of the VIG. This individual compact unit contains all the main connections for battery, pantograph and motor as well as the necessary distribution and other functions.

From theory to practice
After numerous tests, such as component-specific individual commissioning and the commissioning of the overall system in an unbuilt state, the real test run of the prototype is due to take place. The vehicle has already undergone several tests on the RWTH test track. As a next step, the pantograph will be tested on another test track to see whether the process of docking to the overhead line runs smoothly.
Afterwards, the prototype will be underway in public traffic so that the research group can carry out comprehensive measurements. "The goal is to further optimize the system and achieve a higher degree of maturity. We want to reach a point where the module drive train building block is not only fully developed but is also of real economic interest. Unless the costs are right, the system will not be utilized. But we are on an excellent way here. The project also has a high social relevance:
We have already had visits from many major supplier companies who were enthusiastic after seeing the prototype. We are curious to see what the future holds for our project but are quite proud of what we have already achieved. And with Webasto we have found a partner that provides us with comprehensive support and works with us to drive forward the decarbonization of freight transport," says Dünnwald in conclusion. And Webasto is also enthusiastic about the cooperation. "We are proud to be a partner in such an innovative project with the potential to massively reduce CO2 emissions in road transport. We look forward to further supporting the project in the future and will gladly provide products and theoretical input at any time," adds Michael Bauer, Vice President Business Line Energy Management at Webasto.