Future
Factory
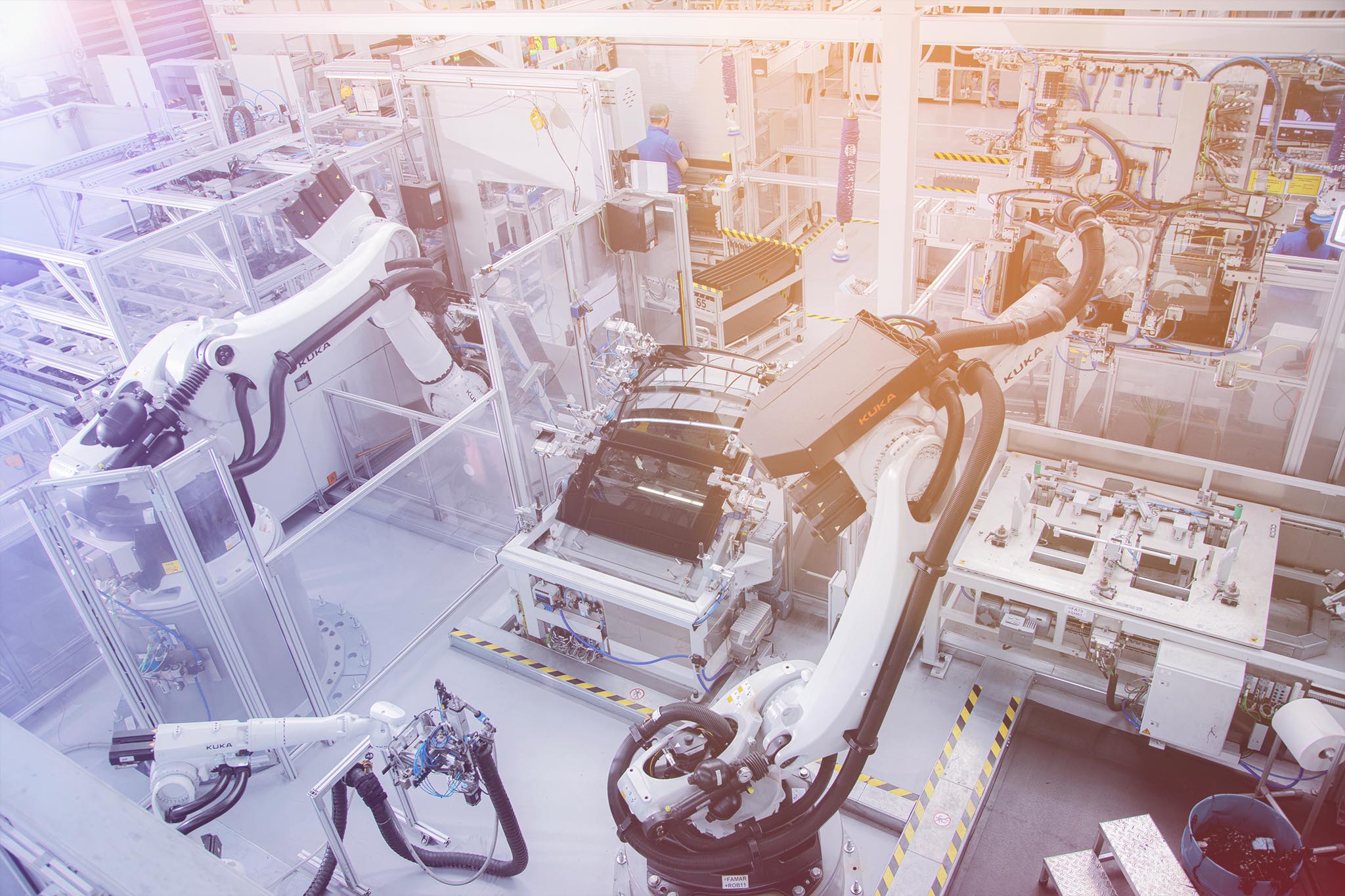
Beyond production lines - Exploring the concept of the future factory
What will the Webasto factories of the future look like? How do Webasto employees work in a smart factory? At Webasto, the concept of a 'Future Factory' encompasses more than production lines and processes. The supply chains, plants, machines and, of course, our employees are also part of the smart Webasto factory of the future. In all these areas, Webasto is focusing on digitalization with the goal of having modern, well-positioned factories.
Global production network
Webasto is a manufacturing company that is represented in all relevant automotive markets worldwide. In the regions of Europe, Americas, and Asia, Webasto has more than 40 production sites - they are the heart of the family-owned company.

Fit for the future
Webasto is a technology company with a long tradition, great enthusiasm for innovations and is continuously evolving. Webasto has successfully established itself in the field of electromobility, and this is accompanied by changes in production requirements. Batteries, for example, are safety-critical products that must be traceable throughout the entire value chain. But new manufacturing technologies, digitalization, increased awareness of the environment and sustainability, and trends set by customers are also influencing the production of Webasto products.
This goes hand in hand with the need for more flexibility and greater willingness to change. At the same time, the requirements for efficiency, quality and on-time delivery are increasing. Webasto wants to set up its plants in the best possible way. This will enable them to respond even faster and more flexibly to (crisis-related) fluctuations, even in a volatile environment. At the same time, Webasto wants to offer its employees a varied, flexible, and attractive workplace.
What is Webasto doing to make its plants 'smart'?
Webasto has a clear roadmap that shows the way to the Webasto plant of the future:
- Building a plant environment that is people-centric
- Use of modular, scalable equipment
- Manufacturing-friendly product design
- Building adaptable infrastructure in plants
- Automation of supply chains
- Automation and digitization of production (paperless manufacturing)
- Establishment of high-performance IT infrastructure and use of cloud services
- Networking of employees
- Focus on sustainability
- Use of analytics and AI tools in production
Our employees are at the center of this. Webasto consistently invests in their further development to build the necessary skills. Webasto employees are already supported in their daily tasks by mobile solutions and smart devices. It is possible, for example, to make complex adjustments to machines remotely using augmented reality glasses. This reduces the travel time of employees who would otherwise be on site and avoids emissions.
What does this mean for Webasto customers?
Fewer errors, faster solutions, and greater efficiency - By creating so-called "digital twins" (a kind of image of the equipment and the plant in virtual space), complex new production lines can be simulated virtually before commissioning. This enables Webasto to design them optimally, and the margin for error is reduced. To get a better impression, virtual reality goggles are used. This allows the user to "dive" into the virtual world. Another advantage of using digital twins is the improvement of machine availability and performance. With the help of the digital twin, production lines, material flows and processes can be analyzed much more precisely, and improvement opportunities are easier to identify. A concrete example is the cycle time of production lines: With the help of digital data, hidden patterns are identified, and performance can be improved much faster compared to manual data collection - making manufacturing processes more efficient.
At the same time, transparency is increased: not only in the own production of Webasto, but across the entire value chain.
- More resilience
- Sustainability and legal standards